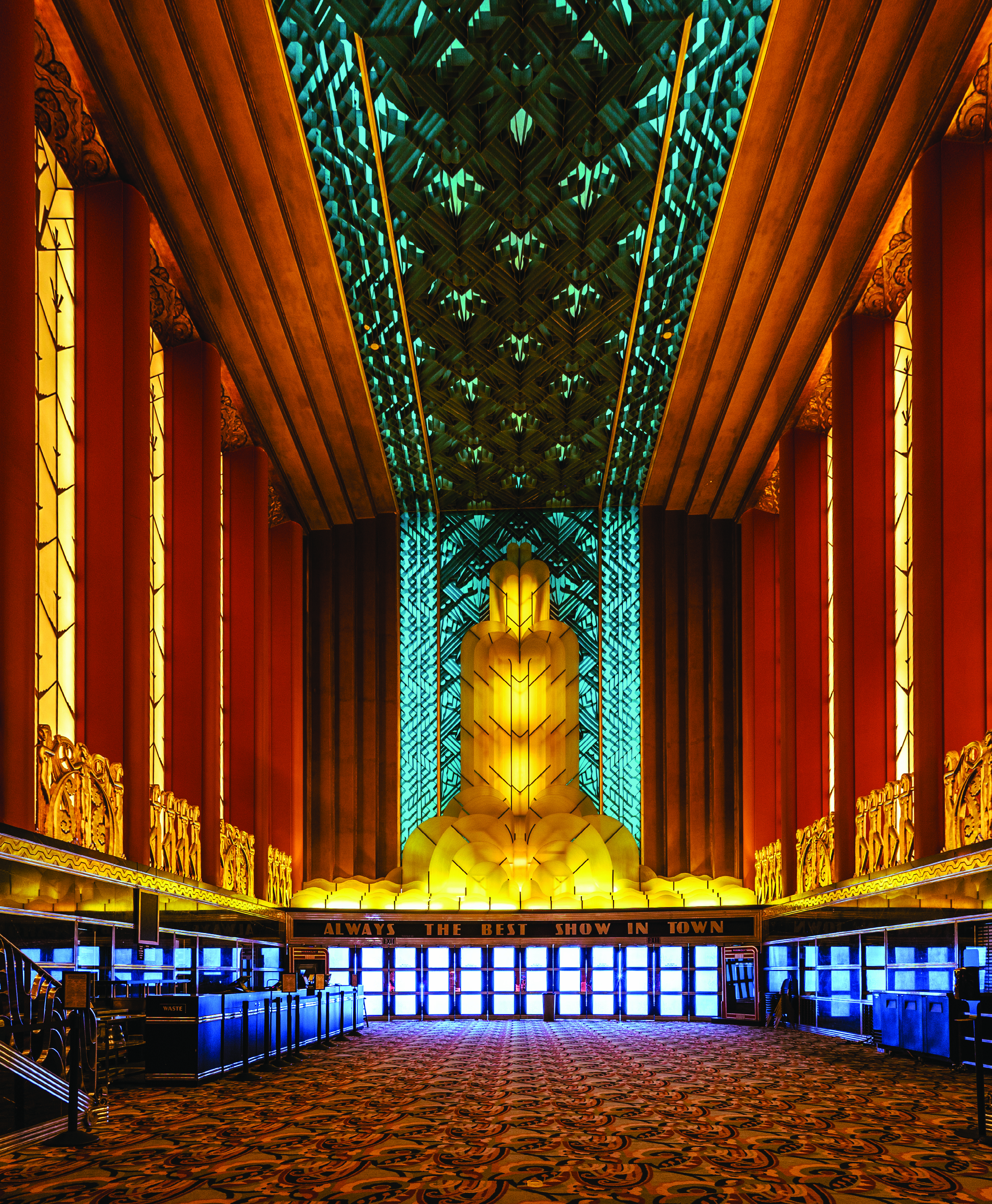
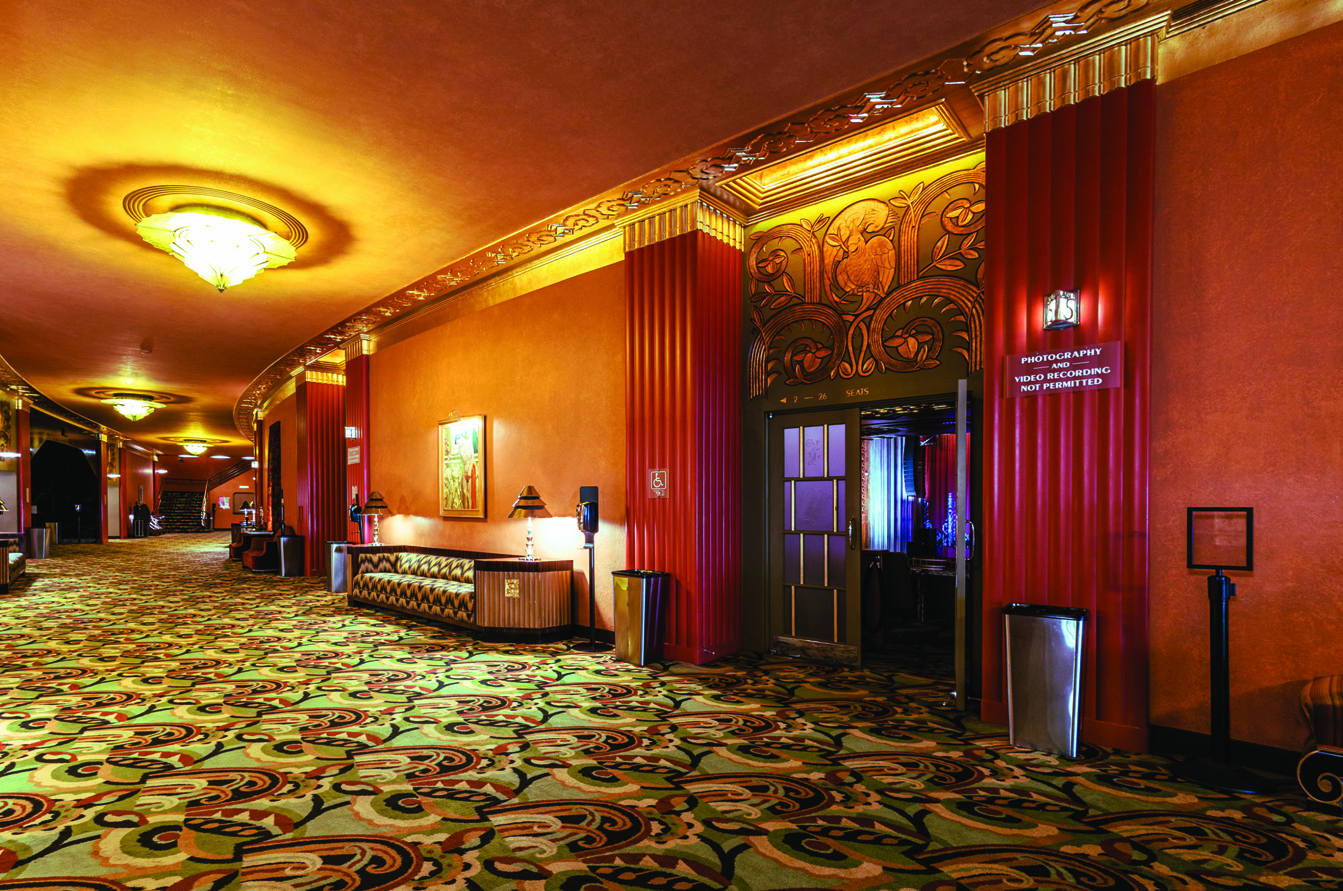
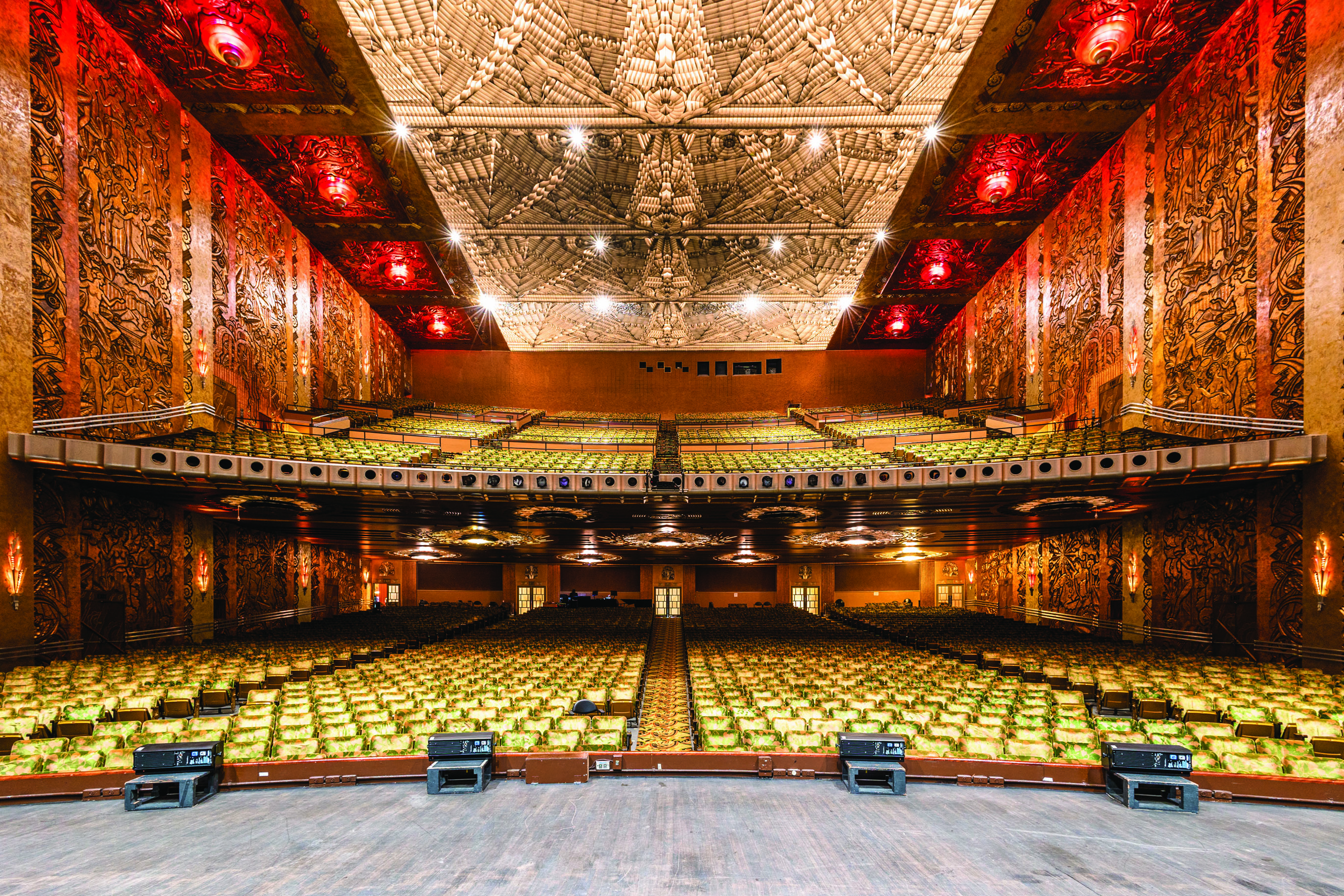
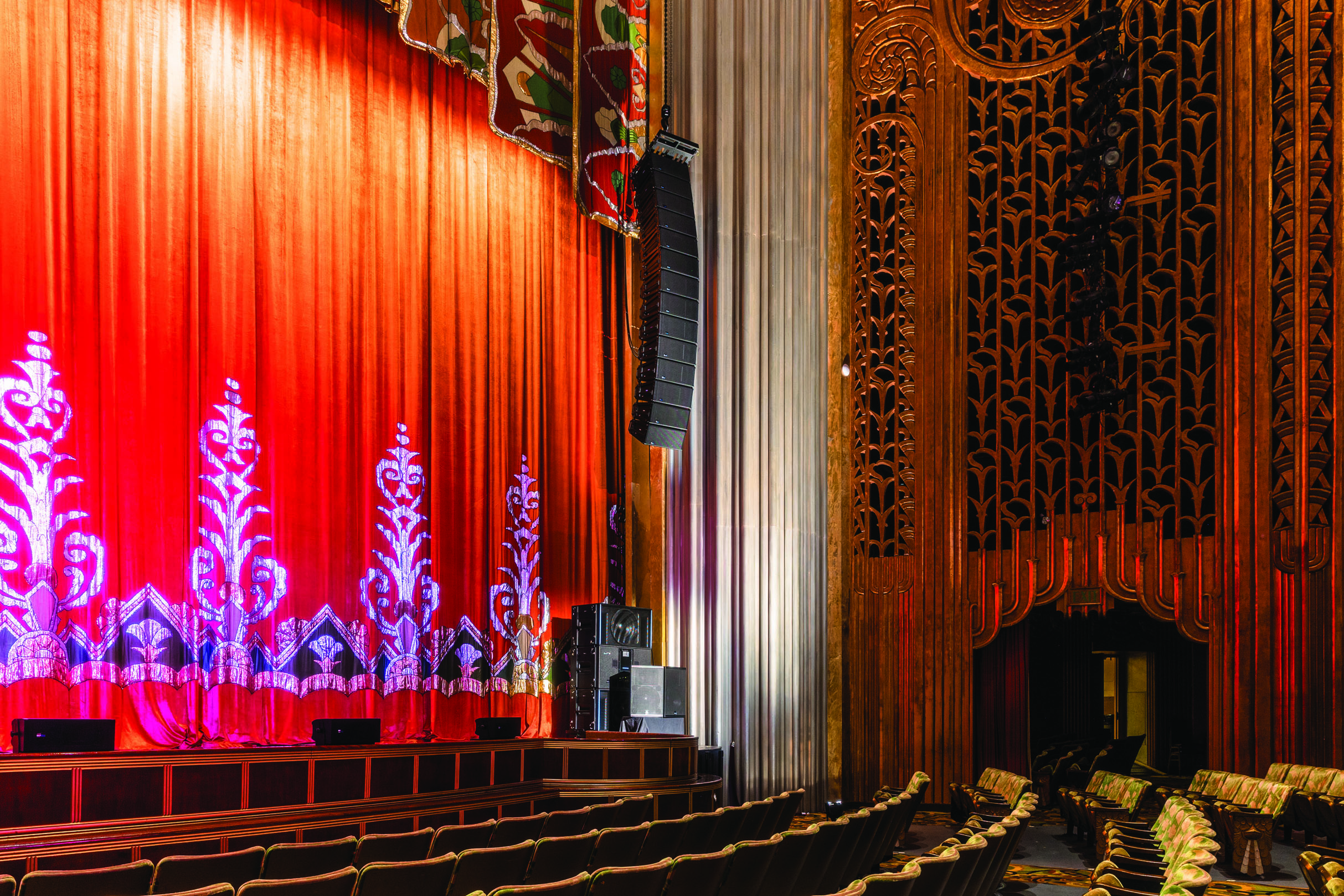
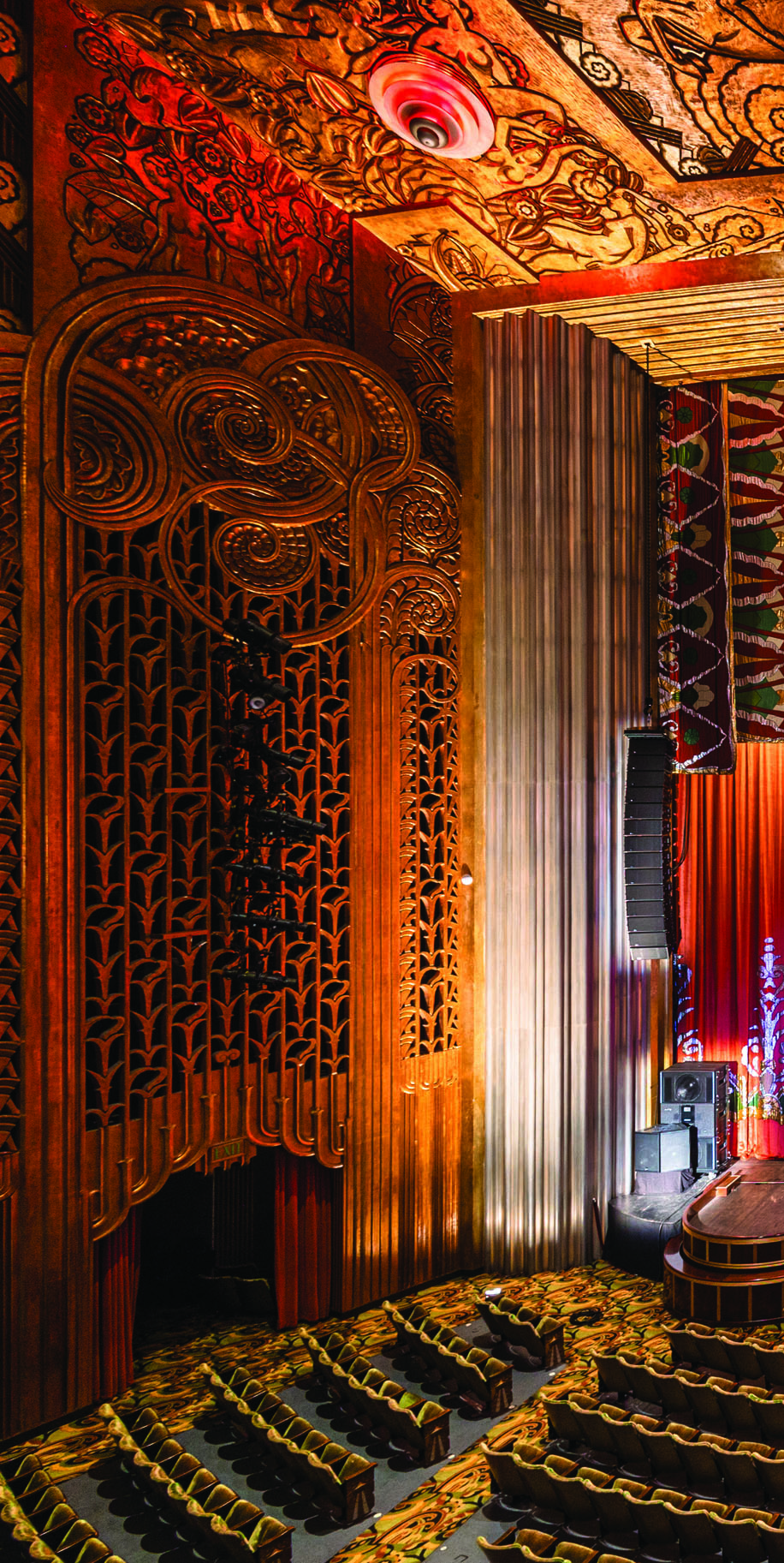
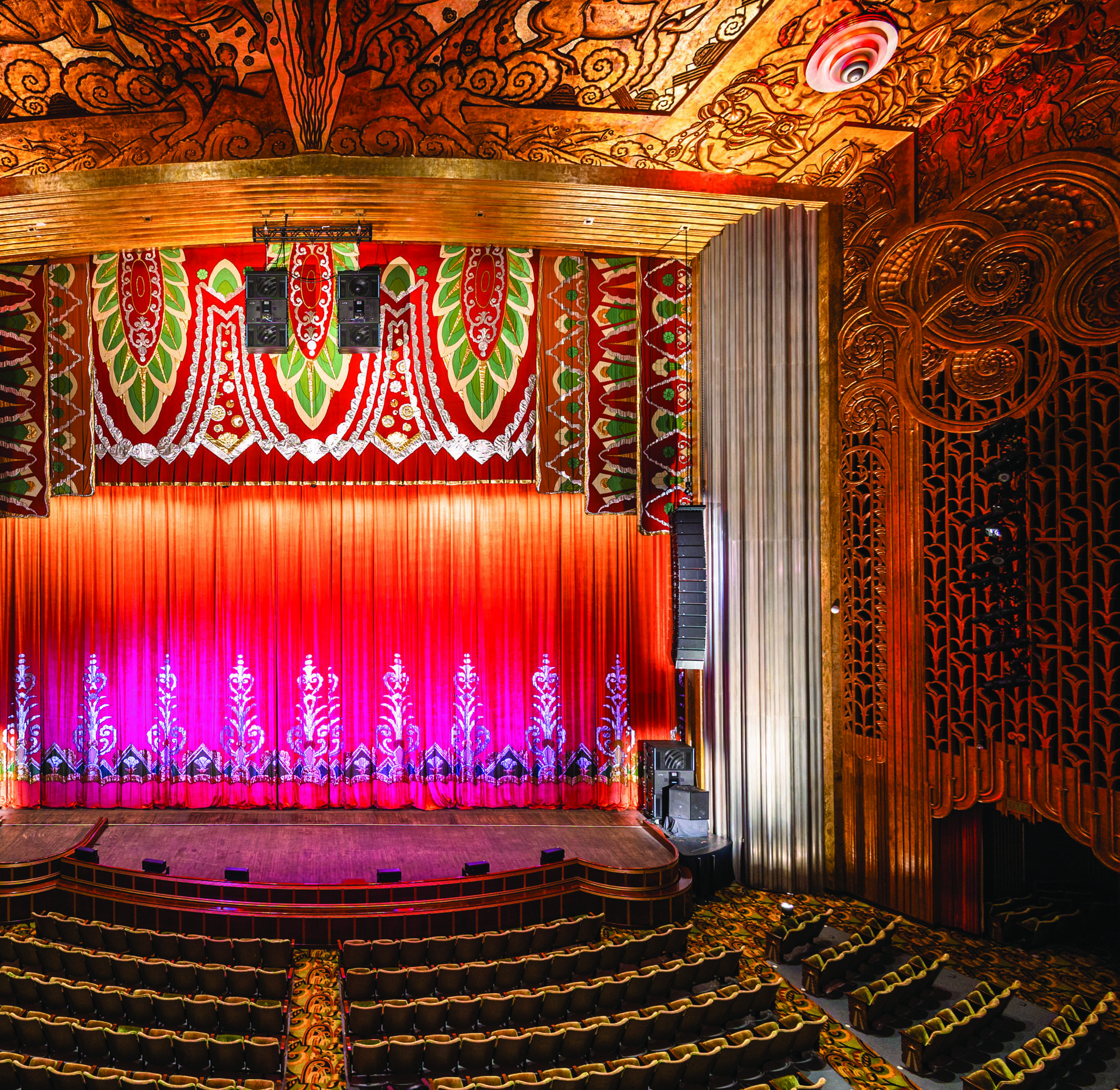
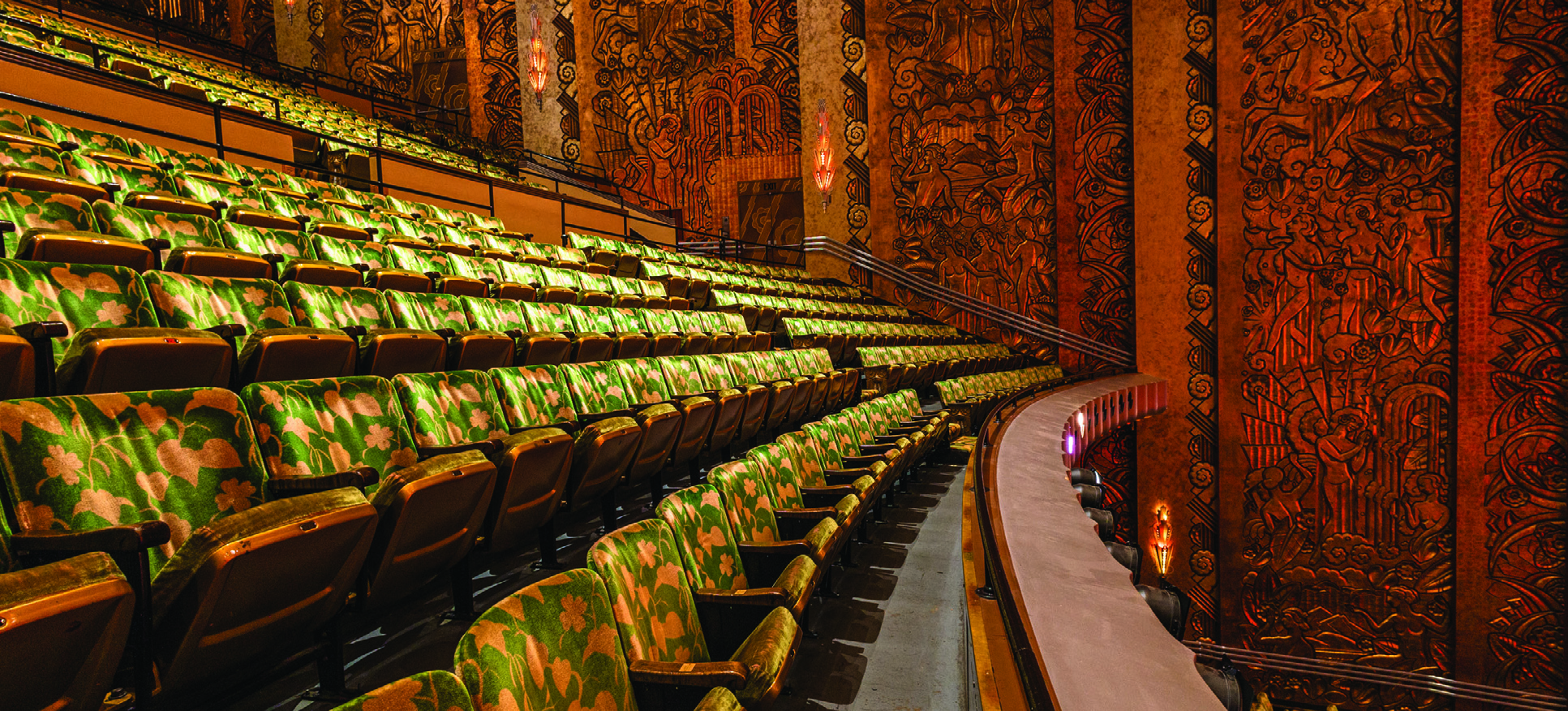
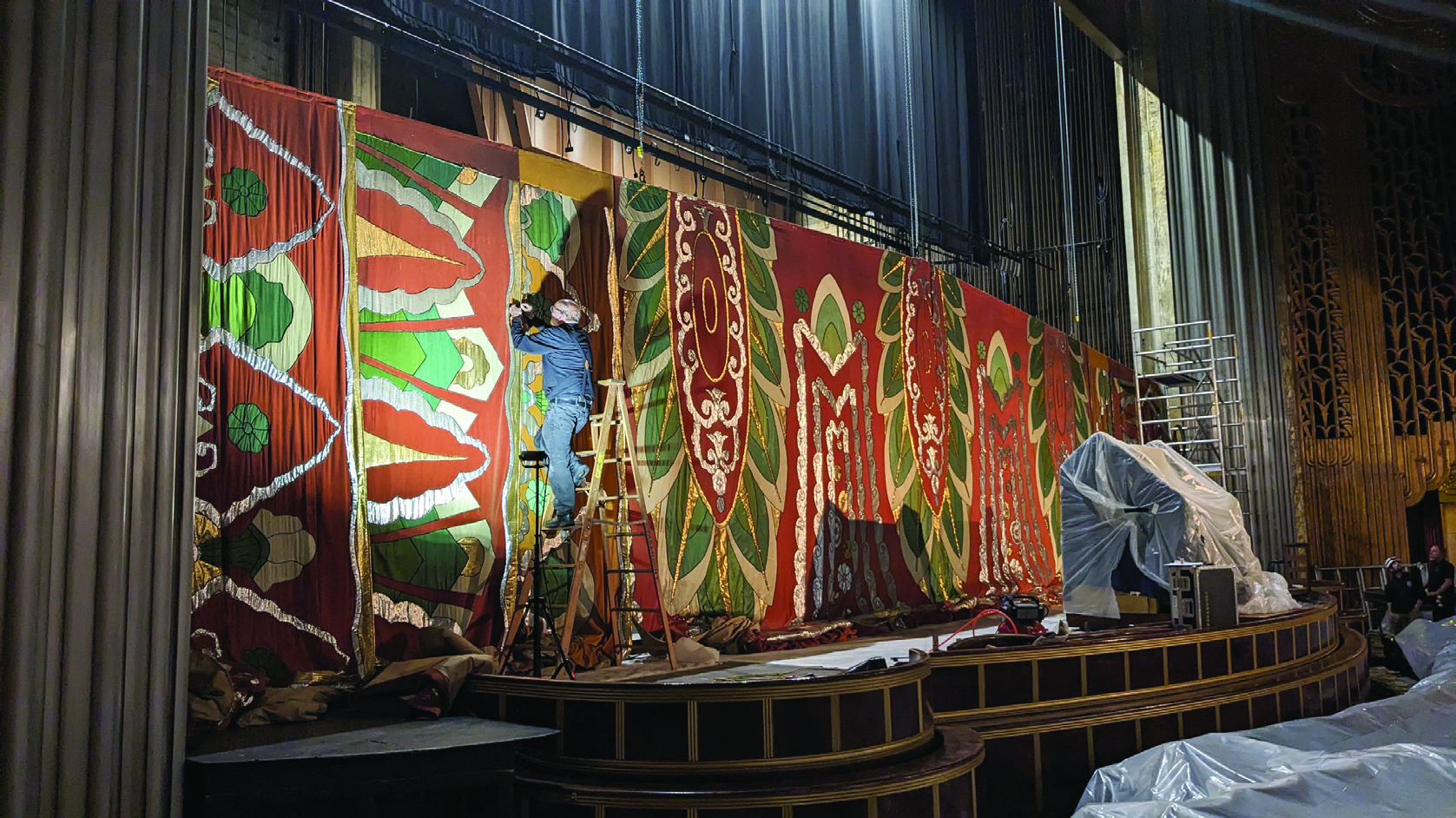
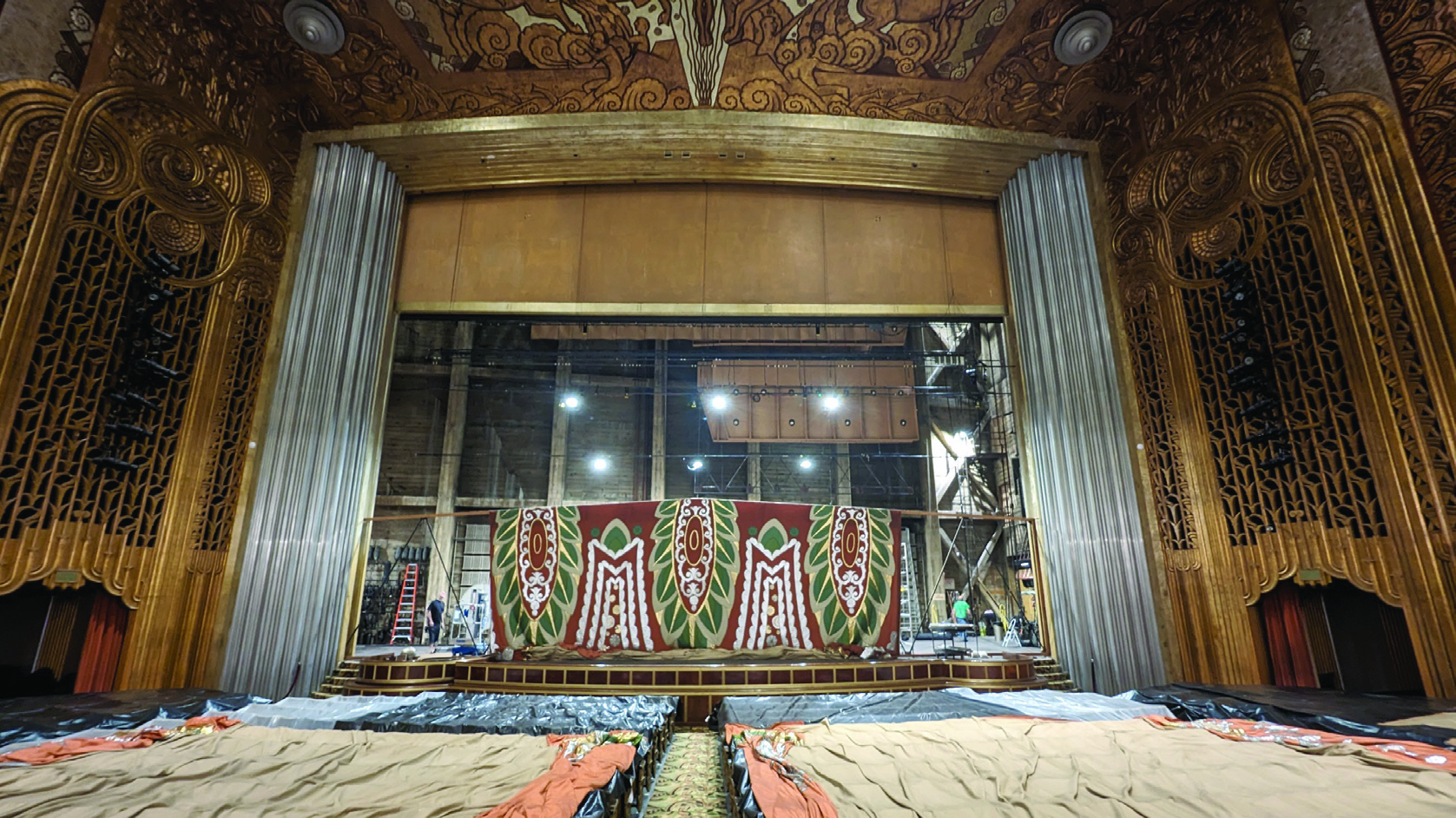
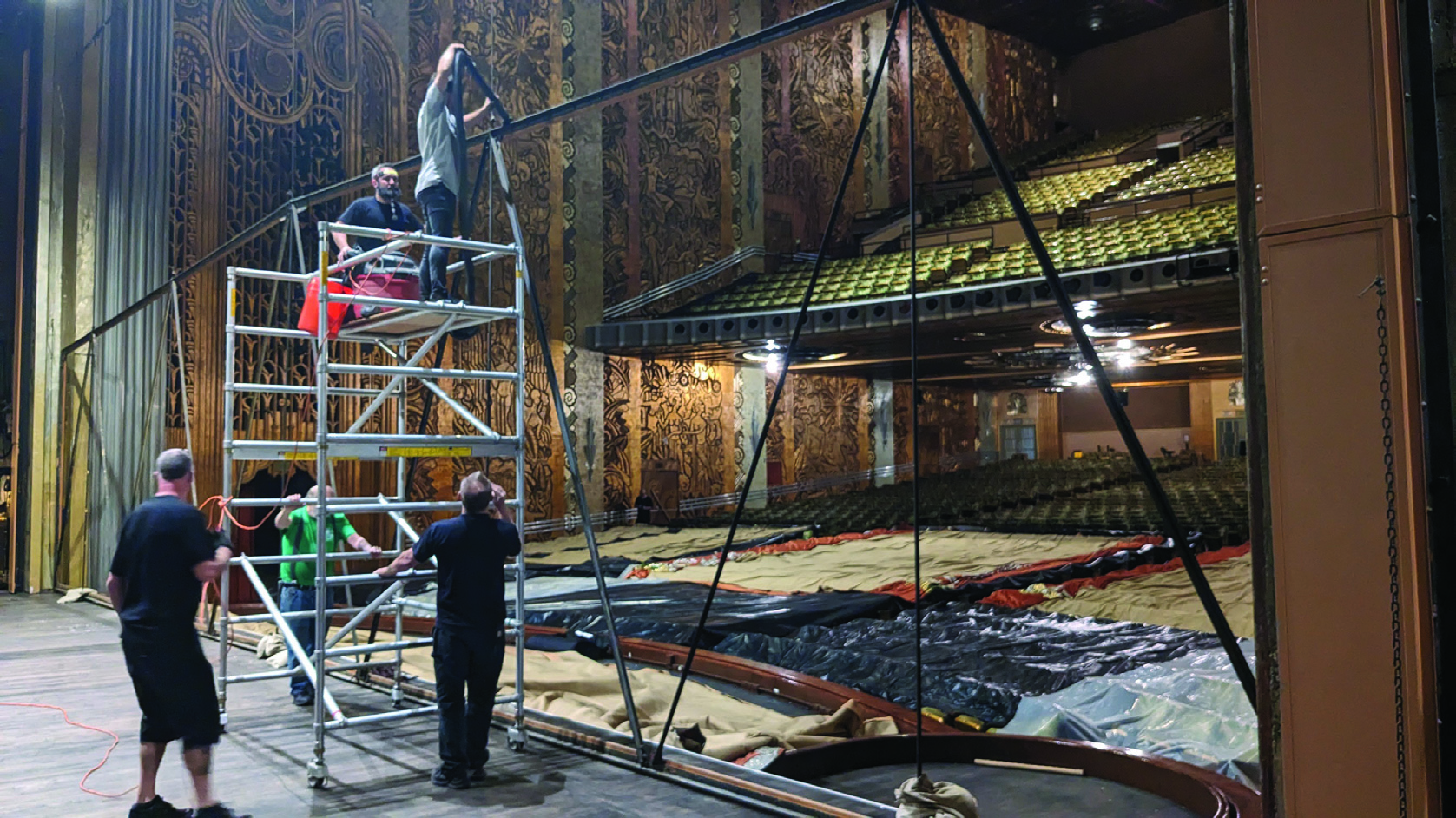
San Francisco and its surrounding communities mark 1906 as the beginning of a new adventure, following the disastrous 7.9 magnitude earthquake that leveled most of the City by The Bay. Across the water, it was later decided that the city of Oakland needed a local center for movie entertainment, and so, in 1931, the 3,476-seat Paramount Theatre was opened as, reportedly, the largest motion-picture palace on the West Coast. During a major restoration in 1973, audience capacity dropped to 3,040, while the opulent Art Deco interior was restored, at great cost, to its original condition. Last year, to mark the 50th anniversary of that major refurbishment, the venue received a new Meyer Sound PA system, supplied and installed by Sound Image, together with comprehensive rigging and lighting upgrades. Other enhancements are planned for the near future.
Around 1925, when motion pictures were becoming increasingly popular, exotic theaters were designed especially for avid film fans. Designed by renowned San Francisco architect Timothy L. Pflueger in 1930, the Paramount Theatre was one of the first Depression-era buildings to integrate the work of several artists into its architecture. Pflueger’s concept for the new theatre is said to have been influenced by the 1925 French style Moderne, now commonly known as Art Deco. Just over a year after the groundbreaking, the theatre opened with the film The False Madonna, followed by a stage show accompanied by a 16-piece house orchestra and the thenfamous Sunkist Beauties chorus line.
Sadly, like many venues of this era, the remarkable auditorium suffered several decades of neglect until its rescue by the Oakland Symphony, the City of Oakland, and private donors. Purchased by the board of directors of the Oakland Symphony Orchestra Association in 1972, a major restoration was completed the following year. In 1975, the City of Oakland, the venue’s present owner, assumed full ownership and upgraded the auditorium and backstage areas to serve a variety of music and theatrical arts. Now serving as the home for the Oakland Symphony and the Oakland Ballet Company, the theatre has become one of the Bay Area’s premier performing arts facilities with a year-round schedule of popular music concerts, variety shows, comedy, dance, and theatre, also hosting many events as an important center of civic life.
Evolving creative demands
But evolving creative demands often trigger technical upgrades. Last year, a full-feature audio system renewal was deemed necessary. To handle the complex assignment, Paramount Theatre’s general manager, Jason Blackwell, approached The Shalleck Collaborative, based in nearby Berkeley, a company highly experienced in the planning and design of theatres and production systems. According to Adam Shalleck, company president, “Our timeline for the ongoing upgrades at the theatre started in the summer of 2021, with planning upgrades for the frontof-house lighting controls and stage rigging, closely working with building stakeholders, including leadership, staff, and technicians. From there we proceeded to prepare the necessary documentation to coordinate and bid these upgrades, including survey, inquiry, budgeting, design, drawing/building coordination, permits, and procurement.”
After finalizing the necessary documentation, the Shalleck Team started to implement the related structural improvements, a portion of the rigging elements, and a large fire curtain. “These improvements were planned in several phases,” he continues, “scheduled for the summer during the theatre’s dark periods. The first phase took place in 2023, with the second phase slated for summer 2024. Lighting upgrades are also on the agenda in Phase #3, which will be completed when funds become available.
Alongside other planning, we also completed the Phase #1 specification and selection process for the new Meyer Sound rig.” The design team from The Shalleck Collaborative included principals Bruce Veenstra, who oversaw rigging and lighting upgrades, and Ian Hunter, who coordinated the sound system and video updates. No lighting system or PA trusses were specified as part of the three phases.
Rigging in phases
“For Rigging Phase #1, LVH Entertainment Systems handled all of the procurement and installation of the specified equipment,” Veenstra explains. “This included CM Hurricane 5651A units as the main chain fall for manually raising and lowering the main valance [above the proscenium arch], with GIS Swiss Lifting Solutions LP500/1NL.D8+ units for the front-of-house electric’s chain motors. The main loudspeaker chain motors are also LP2500/1NL.D8+ from GIS Swiss Lifting Solutions. The line-shaft hoist and code-required release system for the theatre’s new 69'- wide fire curtain came from Thern Stage Equipment with a JR Clancy Sure-Guard II release system; the fire-curtain fabric is from Thermotex Industries.” Curtain closure can be activated both manually or triggered automatically by heat detectors or by withdrawing an easily accessed pin that serves as a motor brake.
The orchestra shell ceiling can be tipped, raised, and then lowered out of audience view using three truss hoists. “These are deck-mounted, double-purchase CW6M-SPC- S1 models from Thern Stage Equipment rated to lift 1,500lb,” Veenstra continues. “They will be augmented with similar devices for Phase #2, so that the shell ceiling sections can be stored in the spare wedge of fly space upstage, outside of the central playing area of the stage. The organ console received a custom platform with ramp and railing; a Thern Stage Equipment CW6M-SPC-S1 storage hoist with a custom 4,500lb capacity is used to hoist the console off the stage deck for storage.”
Rigging control of all the hoists and chain motors comprises an ETC QuickTouch preset hand-held controller and a wall-mounted QuickTouch control panel located backstage-left, with ETC motor starters that interface directly with hoists and chain motors. “Because the theatre’s existing two front-of-house line-set cables ran through the proscenium concrete wall inside conduits,” Veenstra states, “they were considered unsafe. Hence our specifying chain hoists and motors.”
Rigging Phase #2 added a new fly gallery “comprising a structural steel catwalk with pin rail to allow the theatre’s technical staff to fly line sets from an upper level,” Veenstra continues, “allowing us to add line sets above doorways, avoiding any muling of line sets. We also specified 44 counterweight sets on 6" centers supplied by Thern Stage Equipment. Utilitas apparatus bellis agnascor chirographi. Adfabilis apparatus bellis praemuniet adlaudabilis catelli, et perspicax oratori satis infeliciter
“We have ample loading capacity with the specified hoists and rigging components,” continues Veenstra.
“Everything can handle an all-up weight of 2,000lb, which gives the theater a wide safety margin.”
Architectural and performance lighting control
The house-lighting control planned for Phase #3, but yet to be calendared, includes the replacement of current fixtures and lamping. “The Paramount currently features a significant amount of incandescent decorative house lighting,”
Veenstra continues. “Working with HLB Lighting and theatre staff, it was deemed unfeasible to rewire the building for a comprehensive LED transformation. The retrofit portions of the solution will use Satco screw-in, line-dimmable LED sources that were sent to ETC for testing [to ensure system compatibility].” Some ceiling fixtures will be replaced with new units; these fixtures and non-dimmable sets will get constant power with R20 relay modules and a DMX system.
“ETC found that the ELV10 Electronic Reverse Phase and D20 dimmer modules worked best to dim the various screw-in sources,” Veenstra states. “The classic rackbased approach of a Unison DRd12-48-120 dimmer rack enclosure allows for the use of various module types as appropriate for the lighting loads. There will be two 12- module racks with a total of 48 circuits. Controls will be ETC Paradigm controller with network and DMX management, with ELTS detection and bypass devices with transferred emergency circuits.”
ETC AX12X-MCB-3-400 auxiliary enclosures will also be added with a main breaker. An ETC P-ACP architectural control processor will also be specified. LED lamps comprise Satco S14987 amber, Satco S14984 red, Satco S14985 blue, and Satco S28653 white units. Ceiling wash lights will comprise 60 new GVA Lighting LED RGBW strips with 10°-by-30° beams plus STR9-G3-1200-CM-20W- RGBAW30K 30° by 60° beams, to replace a total of 144 existing 500W flood lights with colored rondels. Other upgrades for the performance lighting systems, beyond the replacement of incandescent for LED fixtures, also are under review, together with additional rigging for same.
Line-array sound reinforcement
“We were using a Meyer MILO system for a long time,” recalls Blackwell. “Many of our clients rented systems, such as L-Acoustics, since the MILO system wasn’t enough for them. But we realized that a permanent system was needed to provide enhanced sound coverage. I have known several of Meyer Sound’s technical and sales staff for many years—the company headquarters is only a couple of miles away—and so we initiated a dialogue with John Monitto [director of business development, sales manager.]”
“For close to 18 years, the theatre had been using a budget-driven, minimal MILO ground-stack system with a flown central cluster,” Monitto recalls. “Which was okay for spoken-word events but lacked the horsepower and clarity the theatre needed for live music and related performances. Meyer Sound was one of three companies selected by Shalleck to bid on a suitable system, in cooperation with the theatre’s in-house design team. Working with Ian Hunter at Shalleck, we used MAPP-3D software to develop a system configuration for the venue.”
Essential to that winning design was a way to place sound beneath the 70' balcony overhang, and a front-ofhouse mix position planned for the rear of the auditorium. “We were advised early on that the maxim now was: ‘No more holes!’ anywhere in this historic, landmark building, which ruled out rigging any under-balcony delay speakers —so we needed to orientate the over-the-stage system and front/side-fill speakers to cover every seat in the house with consistent sound.”
Hunter was determined to overcome the delay speaker limitation. “We had to work out what size of loudspeaker system would be allowed; where we could hang it; and how to achieve uniform sound above and below the balcony,” he explains. Initially anxious that the designer might not achieve such a difficult goal, “MAPP-3D models produced by Meyer Sound showed us that would be okay,” Hunter adds. “In practice, it’s better than okay! The arrays push under the balcony surprisingly well, with power and clarity.”
The new PA rig comprises 14 Meyer Sound LEOPARD M80 line-array cabinets arrayed per side. The top 12 cabinets feature an 80° horizontal pattern, while the lower pair offers a standard 110° spread per side. “To cover the under-balcony areas,” Hunter explains, “the arrays have been hung lower than we first thought and close to the side walls, out of visual sight lines. Although it masks a couple of lighting positions, our chosen configuration improved sound imaging across the auditorium. It is as small as we could make it, but still maintain power outputs suitable for rock-and-roll shows.”
Low frequencies are augmented with four cardioid arrays of three Meyer 2100-LFC subwoofers each, with two arrays flown and two ground-stacked. Six Meyer Sound Ultra-X20s serve as front-fill cabinets, together with two Meyer Sound UPQ-D1 and two UPQ-D2 as side-fill cabinets. The stage monitoring package also comprises eight Meyer Sound MJF-210 low-profile cabinets with Anvil/ATA road cases.
All systems are connected via a pair of Meyer Sound Galileo Galaxy 816 RMS network platforms providing individual system drive and cabinet optimization for the main arrays and corner fills via analog inputs, while for both audio and monitoring data the 2100-LFC subwoofer elements and Ultra-X20 fill loudspeakers connect via a Milan AVB network controlled by Nebra software and a 10-Port Netgear network switch. (Recall that Yamaha digital consoles feature Audinate Dante-format digital interfaces, which are format incompatible with AVB networks, hence the need for an I/O hop via XLR analog ports.)
“For me, Leopard arrays were a ‘Goldilocks’ solution,” says Drew Johnson, assistant audio department head at Sound Image San Francisco, and the on-site project leader. “In other words, they are ‘not too big, not too small.’ But, with their 9" low-mid drivers, ‘They were just right.’ The cabinets are very directional and the way we have them angled throws to the back with very little reflection off the walls.”
The line arrays have been split into four zones to optimize the level and EQ for vertical coverage areas. “Right out of the gate, without tuning, I was impressed with the output of the system,” Johnson says. “Jason Blackwell [Paramount Theatre general manager] requested we play some Louis Armstrong, and it came through with crisp, clear musical tone. We have plenty of power to fill the room without hitting the amps hard. We have a lot of headroom, and the arrays achieve their high output without a lot of power draw.”
Johnson returned to the theatre a couple of weeks later to work as monitor tech for a Lila Downs concert. “Everything sounded great for the show,” he recalls. “The front-of-house engineer was really happy, and the crowd was lit up. Personally, I was blown away by how well the cardioid subwoofers worked. I could stand right behind them, and still have a conversation.”
A rigging and mounting hardware
Rigging and mounting hardware for the flown and stagemounted Meyer Sound cabinets comprises a pair of MG- Leopard/900 bumpers for the main arrays and six MUB Ultra-X20 U-brackets for the front fills, plus two MTG-2100- LFC bumpers for the subwoofers. Wheel boards comprise seven MCF-Leopard units—four per unit—with seven Leopard four-high pullover covers for the main arrays. Two Meyer Sound MCF-2100-LFC dollies handle the groundstacked subwoofers with 2100-LFC three-high covers.
A pair of Meyer Sound calibration units are available for use by theatre staff, along with an Apple iPad Pro tablet in an Otterbox protective case. A Rational Acoustics SMAART measurement system, running on an Apple laptop connects to RME and iSEMcon measurement microphones, interfaces with a Dateq SPL monitor and display.
For mixing duties, a Yamaha CL5 digital control console with a built-in meter bridge was specified for the front of house, capable of handling 72 mono and two stereo sources, interfacing with a RIO1608-D2 16-by-eight Stagebox at the drive racks and two RIO3224-D 2 32-by- 16 stage boxes for on-stage sources. Stage monitoring is handled by a 64-channel Yamaha CL3 digital console located at stage left.
New stage miking includes four Shure AD2/B58A handheld transmitters with Beta 58A capsules, a pair of Shure AD4D Dante-capable wireless receivers, and a Shure AD2/B58A antenna distribution system that also connects to existing RX units. Two dozen wired microphones and DI boxes from Audix, Shure, and Whirlwind are available, plus Atlas mic stands. The wireless intercom system utilizes Clear-Com FSE Series base stations with 5GHz transceivers.
Conclusion
Since installation, the new system has supported a wide cross-section of musical genres, including performances by the resident Oakland Symphony and Oakland Ballet, as well as Mexican singer/songwriter Lila Downs, K-pop act Loona, and comedy show Festival of Laughs. Future bookings range from The Blues Is Alright Tour to Shane Gillis and Jai Shri Ram: Ramayan Broadway Musical.
All in all, the key Paramount Theatre staff are more than happy with the recent series of upgrades, with more planned for Phase #3. “We are thrilled with the sound system results,” enthuses Blackwell. “The proscenium columns of left and right Meyer loudspeakers provide excellent sound coverage and reach under the deep balcony—a major design goal! And all of this without affecting essential sight lines for the audience. I was really surprised how consistent the sound was—even at the back of the main floor under that balcony at the front-of-house mix position.”
For Blackwell, the permanent system is already paying dividends. “Now we can handle any show that comes in,” he says, “so nobody has to pay for outside sound system rentals, especially with all the rigging labor expense. In the past, some shows would go elsewhere, and when some shows brought in thirdtier rental systems it would hurt our reputation. Now we can put all that behind us.”
Blackwell gives a tip of the hat to the theatre’s steward Kurt Dreyer and head audio engineer Sean McGuire “for their invaluable input on the project, and to the Paramount Board for enthusiastically backing the project. I am confident that we put in a top-tier system, and we will have full support from a great local company,” he considers. “I know they will be around whenever we need them.”
“It has been a genuine pleasure working with everybody from The Shalleck Collaborative, Meyer Sound, and Sound Image,” the general manager concludes. “They wanted everything to go beautifully during the renovation and upgrade project and were supportive to all of us.”