Load cases for stage machinery design according to ANSI E1.6-1
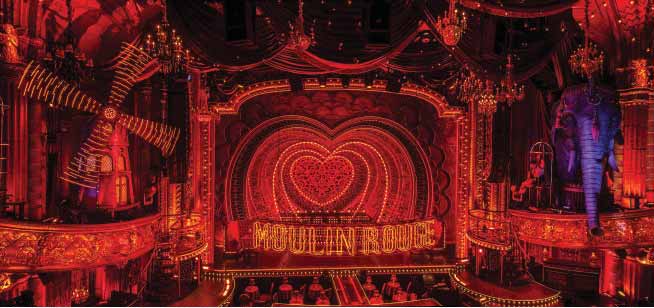
Moulin Rouge! The Musical, now playing on Broadway at the Al Hirschfeld Theatre, has many winches falling within the scope of ANSI E1.6-1. Set design was created by Derek McLane. PRG provided the lighting, sound, and scenic/automation.
ANSI E1.6-1 was first published in 2012 and establishes requirements for the design, manufacturing, installation, and maintenance of powered hoists systems that lift and hold loads over people in entertainment facilities. It is a collaborative effort between stage equipment specifiers, designers, and users around the world, publicly reviewed and revised according to ANSI (American National Standards Institute) regulations to ensure it reflects a consensus among all industry stakeholders.
It is also considered a voluntary standard, as there are no laws in place to enforce it.
However, in the realm of case law, it does serve as documentation of best practices, and manufacturers who choose not to comply can expose themselves, and potentially their customers, to unnecessary risk.
Prior to ANSI E1.6-1, designs for this type of equipment were largely governed by a combination of architects’ specifications and internal shop practices. The process of creating the standard started with convening a group of consultants, engineers, and users to condense the common threads of these many specifications and best practices into a set of design rules. There were consistencies found in the practices of most builders and specifiers, and those requirements became the foundation of the published standard.
However, as the work progressed, it became apparent that merely listing the time-honored prescriptive requirements would not result in a document that would protect the users of the equipment from the changing hazards encountered with ever faster and heavier stage automation machinery. The writers observed that it was important to understand not only what design factors we may be using, but to justify why we use them, and to include a set of rules to advise designers when to increase the strength of components.
ANSI E1.6-1 requires the designers to understand the forces, not only due to the magnitude of the weight attached to the end of the rope, but also those due to effects such as starting, stopping, and even the overload capacity of the machine itself. In engineering parlance, a set of circumstances that result in a distinct change of loads is known as a “load case,” and there are three basic load cases required to be considered by E1.6-1: static load, characteristic load, and peak load. To fully understand the standard, below is the definition of each load as written in E1.6-1.
Static load: The maximum force applied to a component of a hoist system resulting from normal intended operating conditions while the system is at rest. This includes the apportioned fractions of the working load limit (WLL), and self-weight, including that due to load carrying devices and lifting media.
Characteristic load: The maximum force applied to a component of a hoist system resulting from normal intended operating conditions while the system is at rest or in motion. This includes the apportioned fractions of the working load limit (WLL), self-weight including that due to load carrying devices and lifting media, and the forces due to inertia in normal use.
Peak load: The maximum force applied to a component of a hoist system, while the system is at rest or in motion, resulting from abnormal conditions or irregular operation.
(E.g. effects of uncontrolled stops, stalling of the prime mover, or extreme environmental conditions.) The standard anticipates the changes in loads due to motion, and it requires the designer to calculate the effects. Equally as important, the standard requires the designer to calculate the effects not only for when the machine is operating as designed, but also when something abnormal happens.
We can consider an example to show some of the differences between these numbers. Consider a speaker cluster hoist that has a working load limit of 1,000 lb. that is attached to a load carrying device that weighs another 500 lb. Let’s say that it is a fixed speed machine—e.g. no frequency drive or load measurement capabilities— and it moves at a modest speed.
First, start by calculating the static load as the sum of the WLL and the weight of the bumper: Static load = 1,000 lb. + 500 lb. = 1,500 lb.
Next, the characteristic load is the product of the static load and the acceleration factor in normal use. The calculations for hoist starting and stopping forces are beyond the scope of this article so we will skip the math and use a factor of 1.25 to account for those effects. Plugging in those numbers we would see that: Characteristic load = 1,500 lb. x 1.25 = 1,875 lb.
Finally, for the peak load the designer must stop and ask, “What might go wrong?”
The first thing we expect to happen occasionally is an emergency stop. When the red button is pressed, it cuts off the power to the motor and the brakes are applied at the same time. Looking at this particular application we see that for a low, fixed speed machine this is not very different from the dynamics of a normal stop. That is certainly not the case for all machines.
Another abnormal situation we have to consider for peak load is stalling. This is what happens when the speaker snags the edge of the proscenium on the way up, or perhaps a poorly trained person attaches a 4,000 lb. load to our 1,000 lb. hoist. In this case, the motor will draw a large amount of current trying to lift the load, and eventually components within the controller (if designed properly) will open the circuit and stop the machine. However, for a fixed speed machine there is typically a delay associated with this thermal protection and in the meantime, a typical AC motor might generate over three times its rated torque!
Again, we will skip the engineering math, but once those calculations were complete
our peak load would probably look like something this: Peak load = 1,000 lb. x 3.5 = 3,500 lb.
To summarize the results of our load case analysis: We expect to walk into the theatre on an average day and see the 1,500 lb. speakers hanging motionless in the air. The 1,500 lb. hoist is holding is the static load.
We also expect that it won’t be too long before somebody presses the up or down button, and the accelerating forces will increase the load on the hoist to 1,875 lb. This is the characteristic load.
Unfortunately, we all have bad days, and so we must anticipate the possibility that someday the speaker cluster could be snagged on the catwalk, or grossly overloaded in some other way. This is not a very sophisticated hoist, and so the machine would hum loudly for a moment before the thermal relay trips, and in that period, the load grows to 3,500 lb. This is the peak load.
So, after studying our application, we find out that we must design our 1,000 lb. hoist for 3,500 lb., right? Well, yes, but only in a manner of speaking. The underlying philosophy of the standard is that regardless of what happens, the load should not fall. This is not to say that the owner can do whatever they want with the machine! We must anticipate that the machine might get overloaded, but it certainly doesn’t have to lift that overload; it just needs to not be damaged by the overload. The standard reflects this idea by establishing different design factors for each type of component on the hoist and for each of the three load cases.
Consider an example of how the three loads combine with the design factors. According to ANSI E1.6-1, the design factor for wire ropes is 8:1 for the static load, 5:1 for the characteristic load, and 1.33:1 for the peak load. Let’s say I have a rope with static, characteristic, and peak loads of 500, 625, and 2,000 lb., respectively.
Figure 1 shows the combination of the loads in each case with its respective design factor. For this application, the static load controls the design and my rope must have a strength of at least 4,000 lb.
So, why bother with the three cases if you could use the old 8:1 rule on the 500 lb. weight and get the answer? Consider what happens if the artistic director now wants to move that 500 lb. load very quickly. We put a bigger motor and a frequency drive on our machine, and we crank up the speed and acceleration of the hoist.
The static load is the same 500 lb. but increasing the acceleration to 0.7 g drives our characteristic load up to 850 lb. See Figure 2. Note that the characteristic load now controls the design, not the static load, and as a result our faster application requires a larger wire rope even though it is lifting the same load.
Using the three load cases can show the danger of using motors or brakes that are oversized for the application. Oversized brakes tend to increase the stopping forces and drive up the required strength of the hoist components. Oversized motors can do the same for stalling loads. More sophisticated controls, on the other hand, can provide gentle accelerations and more quickly detect overloads. This may reduce the loads and the required strength of the mechanical components.
The point is, when we design and build machinery for automation, we can’t just think of one 500 lb. load. It’s 500 lb. when it is hanging quietly in the air. It might be a 600 or 800 lb. load when we press the go button and depending on how we design the machine and controls, it may turn into a 2,000 lb. load if something goes wrong. The standard requires that the machine designers do the math to figure out exactly what the dynamic forces are, and design the machine for both normal use and reasonably foreseeable misuse. We do not want the load to fall in any of these cases.
Intuitively we understand that higher loads, faster speeds, larger motors, and bigger brakes all tend to increase the risk associated with a hoisting application. ANSI E1.6-1 gives stage machinery designers a method to combine these factors and others to generate reasonable designs that comply with documented industry standards.■
Peter V. Svitavsky, P.E. has worn a number of hats at J.R. Clancy and Wenger Corporation over the last twenty years working on stage engineering projects around the world. He is a licensed Professional Engineer, inventor of several patented designs, and proud to be among the members at USITT and ESTA who work to develop national standards for the entertainment industry. He is a regular contributor to the education of future generations of industry professionals through classes and conferences. When he is not working on stage machinery you will find him with his family at home in the Finger Lakes or prowling in the woods and fields of Upstate New York.
ANSI E1.6-1 gives stage machinery designers a method . . . to generate reasonable designs that comply with documented industry standards.
ANSI E1.6-1 requires the designers to understand the forces . . . due to effects such as starting, stopping, and even the overload capacity of the machine itself.
It is also considered a voluntary standard, as there are no laws in place to enforce it.
However, in the realm of case law, it does serve as documentation of best practices, and manufacturers who choose not to comply can expose themselves, and potentially their customers, to unnecessary risk.
Prior to ANSI E1.6-1, designs for this type of equipment were largely governed by a combination of architects’ specifications and internal shop practices. The process of creating the standard started with convening a group of consultants, engineers, and users to condense the common threads of these many specifications and best practices into a set of design rules. There were consistencies found in the practices of most builders and specifiers, and those requirements became the foundation of the published standard.
However, as the work progressed, it became apparent that merely listing the time-honored prescriptive requirements would not result in a document that would protect the users of the equipment from the changing hazards encountered with ever faster and heavier stage automation machinery. The writers observed that it was important to understand not only what design factors we may be using, but to justify why we use them, and to include a set of rules to advise designers when to increase the strength of components.
ANSI E1.6-1 requires the designers to understand the forces, not only due to the magnitude of the weight attached to the end of the rope, but also those due to effects such as starting, stopping, and even the overload capacity of the machine itself. In engineering parlance, a set of circumstances that result in a distinct change of loads is known as a “load case,” and there are three basic load cases required to be considered by E1.6-1: static load, characteristic load, and peak load. To fully understand the standard, below is the definition of each load as written in E1.6-1.
Static load: The maximum force applied to a component of a hoist system resulting from normal intended operating conditions while the system is at rest. This includes the apportioned fractions of the working load limit (WLL), and self-weight, including that due to load carrying devices and lifting media.
Characteristic load: The maximum force applied to a component of a hoist system resulting from normal intended operating conditions while the system is at rest or in motion. This includes the apportioned fractions of the working load limit (WLL), self-weight including that due to load carrying devices and lifting media, and the forces due to inertia in normal use.
Peak load: The maximum force applied to a component of a hoist system, while the system is at rest or in motion, resulting from abnormal conditions or irregular operation.
(E.g. effects of uncontrolled stops, stalling of the prime mover, or extreme environmental conditions.) The standard anticipates the changes in loads due to motion, and it requires the designer to calculate the effects. Equally as important, the standard requires the designer to calculate the effects not only for when the machine is operating as designed, but also when something abnormal happens.
We can consider an example to show some of the differences between these numbers. Consider a speaker cluster hoist that has a working load limit of 1,000 lb. that is attached to a load carrying device that weighs another 500 lb. Let’s say that it is a fixed speed machine—e.g. no frequency drive or load measurement capabilities— and it moves at a modest speed.
First, start by calculating the static load as the sum of the WLL and the weight of the bumper: Static load = 1,000 lb. + 500 lb. = 1,500 lb.
Next, the characteristic load is the product of the static load and the acceleration factor in normal use. The calculations for hoist starting and stopping forces are beyond the scope of this article so we will skip the math and use a factor of 1.25 to account for those effects. Plugging in those numbers we would see that: Characteristic load = 1,500 lb. x 1.25 = 1,875 lb.
Finally, for the peak load the designer must stop and ask, “What might go wrong?”
The first thing we expect to happen occasionally is an emergency stop. When the red button is pressed, it cuts off the power to the motor and the brakes are applied at the same time. Looking at this particular application we see that for a low, fixed speed machine this is not very different from the dynamics of a normal stop. That is certainly not the case for all machines.
Another abnormal situation we have to consider for peak load is stalling. This is what happens when the speaker snags the edge of the proscenium on the way up, or perhaps a poorly trained person attaches a 4,000 lb. load to our 1,000 lb. hoist. In this case, the motor will draw a large amount of current trying to lift the load, and eventually components within the controller (if designed properly) will open the circuit and stop the machine. However, for a fixed speed machine there is typically a delay associated with this thermal protection and in the meantime, a typical AC motor might generate over three times its rated torque!
Again, we will skip the engineering math, but once those calculations were complete
our peak load would probably look like something this: Peak load = 1,000 lb. x 3.5 = 3,500 lb.
To summarize the results of our load case analysis: We expect to walk into the theatre on an average day and see the 1,500 lb. speakers hanging motionless in the air. The 1,500 lb. hoist is holding is the static load.
We also expect that it won’t be too long before somebody presses the up or down button, and the accelerating forces will increase the load on the hoist to 1,875 lb. This is the characteristic load.
Unfortunately, we all have bad days, and so we must anticipate the possibility that someday the speaker cluster could be snagged on the catwalk, or grossly overloaded in some other way. This is not a very sophisticated hoist, and so the machine would hum loudly for a moment before the thermal relay trips, and in that period, the load grows to 3,500 lb. This is the peak load.
So, after studying our application, we find out that we must design our 1,000 lb. hoist for 3,500 lb., right? Well, yes, but only in a manner of speaking. The underlying philosophy of the standard is that regardless of what happens, the load should not fall. This is not to say that the owner can do whatever they want with the machine! We must anticipate that the machine might get overloaded, but it certainly doesn’t have to lift that overload; it just needs to not be damaged by the overload. The standard reflects this idea by establishing different design factors for each type of component on the hoist and for each of the three load cases.
Consider an example of how the three loads combine with the design factors. According to ANSI E1.6-1, the design factor for wire ropes is 8:1 for the static load, 5:1 for the characteristic load, and 1.33:1 for the peak load. Let’s say I have a rope with static, characteristic, and peak loads of 500, 625, and 2,000 lb., respectively.
Figure 1 shows the combination of the loads in each case with its respective design factor. For this application, the static load controls the design and my rope must have a strength of at least 4,000 lb.
So, why bother with the three cases if you could use the old 8:1 rule on the 500 lb. weight and get the answer? Consider what happens if the artistic director now wants to move that 500 lb. load very quickly. We put a bigger motor and a frequency drive on our machine, and we crank up the speed and acceleration of the hoist.
The static load is the same 500 lb. but increasing the acceleration to 0.7 g drives our characteristic load up to 850 lb. See Figure 2. Note that the characteristic load now controls the design, not the static load, and as a result our faster application requires a larger wire rope even though it is lifting the same load.
Using the three load cases can show the danger of using motors or brakes that are oversized for the application. Oversized brakes tend to increase the stopping forces and drive up the required strength of the hoist components. Oversized motors can do the same for stalling loads. More sophisticated controls, on the other hand, can provide gentle accelerations and more quickly detect overloads. This may reduce the loads and the required strength of the mechanical components.
The point is, when we design and build machinery for automation, we can’t just think of one 500 lb. load. It’s 500 lb. when it is hanging quietly in the air. It might be a 600 or 800 lb. load when we press the go button and depending on how we design the machine and controls, it may turn into a 2,000 lb. load if something goes wrong. The standard requires that the machine designers do the math to figure out exactly what the dynamic forces are, and design the machine for both normal use and reasonably foreseeable misuse. We do not want the load to fall in any of these cases.
Intuitively we understand that higher loads, faster speeds, larger motors, and bigger brakes all tend to increase the risk associated with a hoisting application. ANSI E1.6-1 gives stage machinery designers a method to combine these factors and others to generate reasonable designs that comply with documented industry standards.■
Peter V. Svitavsky, P.E. has worn a number of hats at J.R. Clancy and Wenger Corporation over the last twenty years working on stage engineering projects around the world. He is a licensed Professional Engineer, inventor of several patented designs, and proud to be among the members at USITT and ESTA who work to develop national standards for the entertainment industry. He is a regular contributor to the education of future generations of industry professionals through classes and conferences. When he is not working on stage machinery you will find him with his family at home in the Finger Lakes or prowling in the woods and fields of Upstate New York.
ANSI E1.6-1 gives stage machinery designers a method . . . to generate reasonable designs that comply with documented industry standards.
ANSI E1.6-1 requires the designers to understand the forces . . . due to effects such as starting, stopping, and even the overload capacity of the machine itself.