Bringing a dynamic experience to live events
From award shows to stadium concerts, robotic technology adds a layer of dynamic excitement. ProSight Specialty Insurance keeps pace with risk solutions tailored for technical precision.
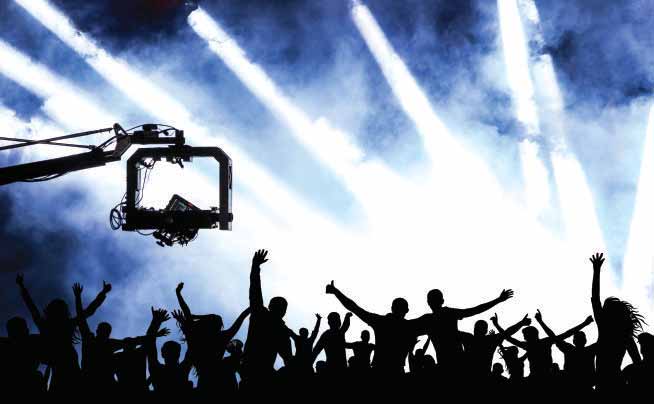
A remotely controlled, crane-mounted camera can provide exciting dynamic images for IMAG or a remote audience.
CAMERAS GLIDING ACROSS THE EDGE of a stage, performers flying overhead on cables, video walls and scenery moving in and out, and cast and crew interacting with stage-mounted toasters, turntables, elevators, and treadmills. Each of these scenarios have one thing in common: robotics. The use of remote-operated equipment at live events is rapidly expanding, which means the exposures that could potentially result in damage to property—or an injury to cast, crew, or patrons—are increasing, too.
Since no two robotic applications are identical, the deployment of these complex systems requires significant planning and preparation by skilled professionals. It is imperative, however, that the planning addresses two equally critical components: (1) functionality that satisfies the creative vision of the client; and, (2) risk management that identifies all foreseeable risks and effectively eliminates or controls these potential occurrences.
Focusing on the big picture
Most companies leading the charge in the robotics era are wellequipped to engineer and fabricate custom-designed components that will enable the systems to perform the functions desired by the client. An important consideration for all such in-house fabrications is to ensure that these mechanical systems conform to all applicable standards. While many of these companies are highly skilled at designing and engineering innovative mechanical systems, they may not be as well-versed on the standards that apply to the safe operation of such mechanical systems. So, for companies that may consider in-house fabrication of system components, it’s important to consult with a product liability expert to ensure that foreseeable exposures related to the operation of the device are either eliminated or adequately controlled.
When creating these complex mechanical systems, it’s not unusual to use components acquired from foreign manufacturers.
Due to certain difficulties in litigating product liability issues against foreign manufacturers, the first domestic handler of a product manufactured outside of the US may often be held solely accountable for the safety of such a product. As such, it’s imperative that product liability exposures for each component directly imported from a foreign manufacturer be assessed, keeping in mind that foreseeable uses and misuses must be anticipated. It’s important to ensure that all such exposures have been formally addressed and have been minimized or eliminated in a manner consistent with applicable requirements. An effective means of minimizing this exposure is to obtain the component from a domestic distributor, which would likely be primarily responsible for the safety of the component.
Employing critical safety steps
Once the customer’s requirements have been identified and the robotic system components have been assembled, it’s time to install the various components at the venue. In such circumstances, it’s not unusual for a contractor to be charged a fee for damages they did not cause. It’s an important step in the process to send an individual out ahead of the installation crew to formally document any existing deficiencies. To minimize the potential for unfounded claims of property damage, a formal, documented inspection of the interior and exterior of the site prior to load-in should be conducted and any such deficiencies (cracks in the sidewalk, holes in walls, broken drinking fountain, damaged carpet, torn upholstery, damaged light fixtures, hand rails, curbs, landscaping, etc.) should be documented to minimize the potential for alleged responsibility once the event is over.
During the design phase of the robotic system, it’s imperative that the plans for any load-bearing components of the finished system be approved (stamped) by a Professional Engineer (PE) to confirm the structural integrity of the system. Similarly, a PE’s formal approval should also be obtained in all circumstances when elements of the robotic system are required to tie in to any structural component of the venue. Written agreement from the venue should always be obtained if any components of the system are to be affixed to walls, floors, or other building interior elements not intended for providing support for theatrical fixtures.
It’s not uncommon to use a third-party contractor to participate in the installation of these systems. In all such circumstances it’s imperative that the contractor be required to provide proof of insurance. Your insurance broker can advise you as to what coverage limits should be required. To further minimize your exposure, the contractor should be required to name you as additional insured. Again, your insurance broker will be able to advise you as to how to accomplish this.
During all tests, rehearsals, and the actual event itself, it’s important that the person overseeing the robotic motion has clear line-of-sight with the entire area over which the components will move. An overly exuberant fa
n, an errant beach ball, or falling stage props could foreseeably affect the pre-programmed movement of the robotic components. Line-of-sight supervision would ensure the ability to stop the movement before an incident occurs.
While it is reasonable that you should be responsible to repair or replace any defective component in the robotic assembly to return the system to proper working order, it’s important to ensure you are indemnified from any consequential damages (such as delay or cancellation of a show, etc.) as a result of such a failure. The terms and conditions document signed by you should be worded in such a way as to limit your liability to the replacement of defective equipment only. Another word of caution is to beware of contracts with subjective wording concerning your responsibilities and scope of duties on behalf of your customer. We strongly recommend having your attorney review such language.
Insuring the possibilities
With all the potential robotic risk scenarios that could occur, companies in the robotics field should have General Liability, Workers’ Compensation, and Auto coverages. They also should strongly consider Inland Marine Coverage for the Property, including Replacement Cost. It should be an All Risk Policy Including Earthquake and Flood, which ProSight Specialty Insurance provides as experts in the media industry. Included within ProSight’s Inland Marine policies are the following pertinent coverages for operations of this type: computer hardware and electronic media, confiscation or destruction, drones, expediting expense, extra expense—production or event delay, loss of rental income, and rental reimbursement. Additional Limits for mechanical breakdown, loss of use, extra expense, and other coverages may be available subject to underwriting and additional premium.
As technology and equipment continually evolve, ProSight is leading the way in live media. With coverage for equipment breakdown, loss of use, and all those little “big” things that often get forgotten on set, we are going above and beyond to provide insurance peace of mind from first act to closing scene.
Mike Kelly is Media Loss Control Manager for Live Events and Film programs at ProSight Specialty Insurance. He earned his bachelor’s degree from California State University at Long Beach and has more than 30 years of experience in entertainment insurance. He can be reached at mkelly@prosightspecialty.com.
Since no two robotic applications are identical, the deployment of these complex systems requires significant planning and preparation by skilled professionals. It is imperative, however, that the planning addresses two equally critical components: (1) functionality that satisfies the creative vision of the client; and, (2) risk management that identifies all foreseeable risks and effectively eliminates or controls these potential occurrences.
Focusing on the big picture
Most companies leading the charge in the robotics era are wellequipped to engineer and fabricate custom-designed components that will enable the systems to perform the functions desired by the client. An important consideration for all such in-house fabrications is to ensure that these mechanical systems conform to all applicable standards. While many of these companies are highly skilled at designing and engineering innovative mechanical systems, they may not be as well-versed on the standards that apply to the safe operation of such mechanical systems. So, for companies that may consider in-house fabrication of system components, it’s important to consult with a product liability expert to ensure that foreseeable exposures related to the operation of the device are either eliminated or adequately controlled.
When creating these complex mechanical systems, it’s not unusual to use components acquired from foreign manufacturers.
Due to certain difficulties in litigating product liability issues against foreign manufacturers, the first domestic handler of a product manufactured outside of the US may often be held solely accountable for the safety of such a product. As such, it’s imperative that product liability exposures for each component directly imported from a foreign manufacturer be assessed, keeping in mind that foreseeable uses and misuses must be anticipated. It’s important to ensure that all such exposures have been formally addressed and have been minimized or eliminated in a manner consistent with applicable requirements. An effective means of minimizing this exposure is to obtain the component from a domestic distributor, which would likely be primarily responsible for the safety of the component.
Employing critical safety steps
Once the customer’s requirements have been identified and the robotic system components have been assembled, it’s time to install the various components at the venue. In such circumstances, it’s not unusual for a contractor to be charged a fee for damages they did not cause. It’s an important step in the process to send an individual out ahead of the installation crew to formally document any existing deficiencies. To minimize the potential for unfounded claims of property damage, a formal, documented inspection of the interior and exterior of the site prior to load-in should be conducted and any such deficiencies (cracks in the sidewalk, holes in walls, broken drinking fountain, damaged carpet, torn upholstery, damaged light fixtures, hand rails, curbs, landscaping, etc.) should be documented to minimize the potential for alleged responsibility once the event is over.
During the design phase of the robotic system, it’s imperative that the plans for any load-bearing components of the finished system be approved (stamped) by a Professional Engineer (PE) to confirm the structural integrity of the system. Similarly, a PE’s formal approval should also be obtained in all circumstances when elements of the robotic system are required to tie in to any structural component of the venue. Written agreement from the venue should always be obtained if any components of the system are to be affixed to walls, floors, or other building interior elements not intended for providing support for theatrical fixtures.
It’s not uncommon to use a third-party contractor to participate in the installation of these systems. In all such circumstances it’s imperative that the contractor be required to provide proof of insurance. Your insurance broker can advise you as to what coverage limits should be required. To further minimize your exposure, the contractor should be required to name you as additional insured. Again, your insurance broker will be able to advise you as to how to accomplish this.
During all tests, rehearsals, and the actual event itself, it’s important that the person overseeing the robotic motion has clear line-of-sight with the entire area over which the components will move. An overly exuberant fa
n, an errant beach ball, or falling stage props could foreseeably affect the pre-programmed movement of the robotic components. Line-of-sight supervision would ensure the ability to stop the movement before an incident occurs.
While it is reasonable that you should be responsible to repair or replace any defective component in the robotic assembly to return the system to proper working order, it’s important to ensure you are indemnified from any consequential damages (such as delay or cancellation of a show, etc.) as a result of such a failure. The terms and conditions document signed by you should be worded in such a way as to limit your liability to the replacement of defective equipment only. Another word of caution is to beware of contracts with subjective wording concerning your responsibilities and scope of duties on behalf of your customer. We strongly recommend having your attorney review such language.
Insuring the possibilities
With all the potential robotic risk scenarios that could occur, companies in the robotics field should have General Liability, Workers’ Compensation, and Auto coverages. They also should strongly consider Inland Marine Coverage for the Property, including Replacement Cost. It should be an All Risk Policy Including Earthquake and Flood, which ProSight Specialty Insurance provides as experts in the media industry. Included within ProSight’s Inland Marine policies are the following pertinent coverages for operations of this type: computer hardware and electronic media, confiscation or destruction, drones, expediting expense, extra expense—production or event delay, loss of rental income, and rental reimbursement. Additional Limits for mechanical breakdown, loss of use, extra expense, and other coverages may be available subject to underwriting and additional premium.
As technology and equipment continually evolve, ProSight is leading the way in live media. With coverage for equipment breakdown, loss of use, and all those little “big” things that often get forgotten on set, we are going above and beyond to provide insurance peace of mind from first act to closing scene.
Mike Kelly is Media Loss Control Manager for Live Events and Film programs at ProSight Specialty Insurance. He earned his bachelor’s degree from California State University at Long Beach and has more than 30 years of experience in entertainment insurance. He can be reached at mkelly@prosightspecialty.com.